Que sistema de dixitalización é adecuado para soldar pelos de cobre en motores eléctricos?
Tecnoloxía de cabelo
A eficiencia do motor de unidade EV é a mesma que a eficiencia de combustible do motor de combustión interna e é o indicador máis importante relacionado directamente co rendemento. Polo tanto, os fabricantes de EV están intentando aumentar a eficiencia do motor reducindo a perda de cobre, que é a maior perda do motor. Entre eles, o método máis eficiente é aumentar o factor de carga do enrolamento do estator. Por este motivo, o método de enrolamento de cabelo aplícase rapidamente á industria.
Cabilas nun estator
O factor de recheo de ranuras eléctricas dos estatores de pel de cabelo rolda o 73% debido á zona de sección transversal rectangular das pelas e ao menor número de enrolamentos. Isto é significativamente maior que cos métodos convencionais, que conseguen aprox. 50%.
Na técnica de pel de pelo, unha pistola de aire comprimida dispara rectángulos preformados de fío de cobre (similares aos pelos) en ranuras no bordo do motor. Para cada estator, entre 160 e 220 pelos hai que procesar dentro de máis de 60 a 120 segundos. Despois disto, os fíos están entrelazados e soldados. É necesaria unha precisión extrema para preservar a condutividade eléctrica das peles.
Os escáneres láser úsanse a miúdo antes deste paso de procesamento. Por exemplo, as pelas de fío de cobre condutivo especialmente eléctrico e térmicamente son frecuentemente desposuídas da capa de revestimento e limpadas por feixe láser. Isto produce un composto de cobre puro sen ningunha influencia interferida de partículas estranxeiras, que pode soportar facilmente as tensións de 800 V. Non obstante, o cobre como material, a pesar dos seus moitos beneficios para a electromobilidade, tamén presenta algúns inconvenientes.
Sistema de soldadura de cabelo Carmanhaas: CHS30
Cos seus elementos ópticos de alta calidade e poderosos e o noso software de soldadura personalizado, o sistema de soldadura de pel de pel de Carmanhaas está dispoñible para o láser multimodo de 6kW e o láser de anel de 8kw, a área de traballo podería ser de 180*180 mm. Procesos facilmente as tarefas que requiren un sensor de vixilancia tamén se poden proporcionar a solicitude. Soldadura inmediatamente despois de facer fotos, sen mecanismo de movemento servo, ciclo de baixa produción.

Sistema de cámaras CCD
• Equipado con cámara industrial de alta resolución de 6 millóns de píxeles, instalación coaxial, pode eliminar os erros causados pola instalación inclinada, a precisión pode chegar a 0,02 mm;
• Pódese combinar con diferentes marcas, cámaras de resolución diferentes, diferentes sistemas de galvanómetro e diferentes fontes de luz, cun alto grao de flexibilidade;
• O software chama directamente á API do programa de control láser, reducindo o tempo para comunicarse co láser e mellorar a eficiencia do sistema;
• Pódese controlar a brecha de suxeición de pin e a desviación de ángulo e pódese pedir automaticamente o procedemento de soldadura correspondente para o pasador de desviación;
• Os pasadores con desviación excesiva pódense saltar e a soldadura de reparación pódese realizar despois do axuste final.
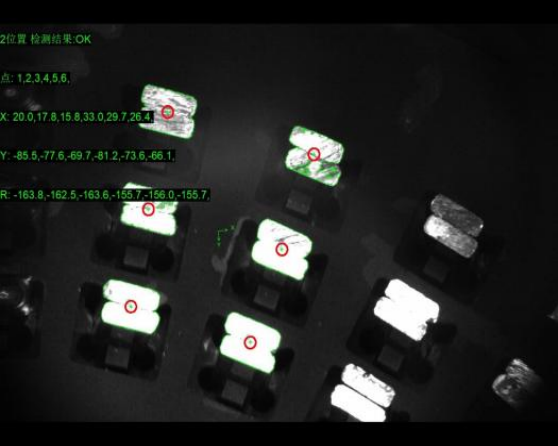
Vantaxes de carmanhaas da soldadura do estator de cabelo
1. Para a industria de soldadura con láser de Hairpin Stator, Carman Haas pode proporcionar unha solución única;
2. O sistema de control de soldadura desenvolvido por si mesmo pode fornecer diferentes modelos de láseres no mercado para facilitar as posteriores actualizacións e transformacións dos clientes;
3. Para a industria de soldadura por láser Stator, establecemos un equipo de I + D dedicado con rica experiencia en produción en masa.
Tempo de publicación: FEB-24-2022